Lot Numbers: The Complete Guide
We'll cover what lot numbers are, how to track them, and why they're so important for small manufacturers.
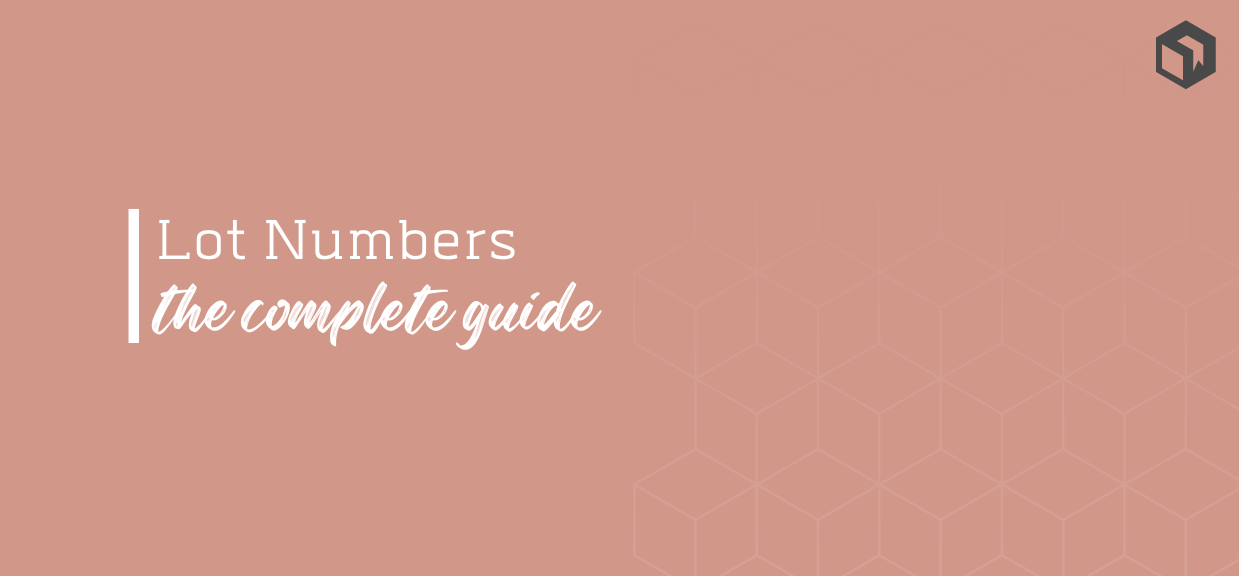
Lot numbers are an important part of any manufacturing process, but they can be especially critical for small manufacturers.
In this complete guide, we’ll cover what lot numbers are, how they’re used, and just why they’re so important.
Along the way, we’ll also provide some handy tips on how to effectively use lot numbers to keep your manufacturing process running smoothly.
Need to get your raw material and product inventory under control?
Try Craftybase - the inventory and manufacturing solution for DTC sellers. Track raw materials and product stock levels (in real time!), lot and batch tracking, COGS, shop floor assignment and much more. It's your small business' production central.
What are Lot Numbers?
Let’s start with some definitions. A lot number is simply a unique identification number assigned to a batch of products. This can be anything from a single item to an entire shipment of goods.
The lot number allows manufacturers to keep track of where products come from and when they were made. It is an essential inventory management technique as it creates full traceability of your stock. For makers that create products that expire (such as food or beverage manufacturers), lot numbers can also help track this information too.
Let’s firstly take a look at the difference between similar tracking codes that are commonly used in inventory management so that we are all on the same page:
Lot numbers and batch numbers are essentially the same thing. They are also commonly known as lot codes, control numbers, or production codes.
Stock Keeping Units (SKUs) are a little bit different as they are unique identifiers for products, while lot numbers identify batches of products. SKUs track individual items, while lot numbers can be used to track an entire shipment of items.
Serial numbers are similar to lot numbers, but like a Stock Keeping Unit (SKU) they are typically assigned to individual items rather than batches of products.
Why are Lot Numbers Important?
Alright, now that we know exactly what a lot number is, let’s take a look at why we should care about these little codes.
Let’s use a typical situation to illustrate: imagine you have just received an email from one of your raw material suppliers. In this message, they indicate that they have discovered a contamination issue with one of the materials they sell that you have previously purchased. They are thus undertaking a full recall of the material and ask you to comply.
The email indicates that you need to do the following:
- Locate any impacted materials you still had on hand and either dispose or return to the vendor
- Identify any products on hand that have been made using this material and dispose if found
- Identify any products already sold to customers that have been made using this material and advise the customer to cease using the product immediately.
Sounds daunting right? With consistent traceable record-keeping processes in place, it is completely possible to locate these products and customers quickly and efficiently.
The key part of traceable record-keeping is Lot Numbers - these are unique identifiers assigned to specific quantities of the materials you purchase and the products you make. By creating a manufacture tracking system that records lot numbers, you’ll be able to see exactly what materials were used in each of the products you have sold.
Lot numbers are important because they allow manufacturers to track their products through the entire supply chain from start to finish.
By knowing the lot number of a product, manufacturers can easily find out when it was made and where it came from. This information can be critical for a number of other reasons too:
Industry and regulatory compliance
Depending on the products you sell and/or the locations you sell to, there may be regulations that you need to adhere to that require you to keep full auditable records of your material usage. As an example, recently the EU introduced the GPSR which requires all online sellers to keep and provide full traceability records.
Quality Control / Quality Assurance
Lot numbers can provide valuable information during an investigation of a product complaint or failure. The lot number can help identify when the product was made, who made it, and what materials were used.
This information can be used to determine if there are any common factors that may have contributed to the problem and to check other products in the same batch to see if they have a similar issue.
Lot tracking can also be used to ensure that quality standards are maintained for raw materials. As an example, one particular supplier may be consistently providing materials that do not meet your quality standards. By tracking lot numbers, you can quickly identify when these materials were used and take appropriate action to find a new supplier.
Inventory Management
Lot numbers can also be used to simply keep better track of your inventory levels and keep your manufacturing process running smoothly.
By knowing how much product you have in stock, and when it was made, you can ensure that you are using and selling the right materials and products at the optimum time.
Fast Material Recalls
If a raw material is recalled by a supplier, lot tracking can be used to identify which products are affected and need to be removed from inventory. This information can be used to quickly locate and remove the affected products from your premises, and also to contact customers who may have purchased these products.
Improved Customer Service
Lot tracking can also be important for customer service. If a customer has an issue with a product, lot numbers can be used to quickly track the product back to its point of manufacture. This information can then be used to correct the issue, prevent it from happening again and keep the customer fully informed.
How are Lot Numbers Used?
There are many ways lot numbers can be used, but the most common use is to track products throughout the manufacturing process. By creating a lot tracking process for both materials and products, it is possible to see:
- When raw materials were received
- Which products were made with those materials
- When products were shipped and who they were shipped to
Lot numbers can also be used in conjunction with inventory management systems, utilizing barcodes, QR codes or RFID tags to automate the tracking process (we’ll discuss a little more about inventory management later in this article).
How to create a lot number
Now that you have the background details on lot numbers, let’s start getting into the nitty gritty on how they are created and used.
For a lot number to be effective, it should be:
- Unique
- Easy to read and to interpret
- Be consistent in terms of numbering and formatting
The actual information included in lot numbers will vary from company to company based on specific workflows and requirements, but there are a few common pieces of information that are often included:
-
The date the product was made
-
The batch or lot number of the raw materials used
-
The sequence number of the product within the lot
As a simple example, your lot numbers might look like this:
- 2022-01-01-001
- 2022-01-02-002
In this example, the lot numbers include the date the product was made (2022-01-01 and 2022-01-02) and the sequence number of the product within the lot (001 and 002). The sequence number would increase with each new product made so that the code is always unique.
How to handle expiration dates
If your products have expiration dates, you can optionally include this information in the lot number as well. This can be done in a few different ways, but the most common is to include the expiration date as part of the lot number. For example:
- 220101-001-EXP230530
- 220101-002-EXP230531
In this example, the lot number would include the product’s date of manufacture, the sequence number of the product within the lot, and the expiration date. The expiration date would be included in all lot numbers so that it is easy to identify when a product expires.
Another common way to include expiration dates is to use a separate field for the lot number and the expiration date. This can be done with a barcode, QR code, or RFID tag. For example:
- lot number: 220101-001
- expiration date: 230531
With this method, the lot number and expiration date are stored in separate fields. This can be helpful if you need to track the lot number and expiration date separately.
What is Lot Tracking?
Lot tracking, also known as batch or batch number tracking, is the process of monitoring and tracing specific groups of products or materials from production to distribution via their lot number.
Lot tracking enables businesses to identify and isolate any potential issues with a specific batch, whether it’s a product recall or quality control. This helps businesses maintain transparency and accountability throughout the supply chain and ensure that customers receive high-quality products consistently.
How to track Lot Numbers
Some small manufacturers start tracking lot numbers using written logs and excel spreadsheets, however as the exact relationship between purchases, manufactures and orders can be quite complex, the use of a spreadsheet can lead to errors and inconsistencies as your business grows.
It is best to use a database as then the relationships can be mapped together correctly - you can either attempt to design this in Access or similar, or purchase specialised lot tracking software like Craftybase.
Whatever system for lot tracking you choose, your written records need to be good enough to be able to quickly generate:
a) Who you purchased a specific batch of materials from and when AND b) Which products were manufactured using this specific batch AND c) Who you eventually sold the products to
This means you’ll want to ensure that you enter in lot numbers for each material purchase that you make, then link this lot number with the manufacture batch you create. Finally, you’ll need to be able to link the manufacture with the customer that purchased the product.
Using inventory software to track your lot numbers
For companies that have a lot of products and raw materials, it can quickly become unwieldy to keep track of lot numbers manually. In these cases, it can be helpful to use either a spreadsheet or specialized software for your lot tracking.
Manufacturing Resource Planning (MRP) software is a type of inventory management software that can be used to generate lot numbers and track lot inventory levels. MRP software is often used by large companies, but there are also many affordable MRP systems available for small businesses.
When lot numbers are generated by MRP software, they are often automatically assigned to products based on the raw materials used and the production date. This can be a helpful way to keep track of lot numbers, but it is important to make sure that the lot numbers are still unique.
Some MRP systems also have the ability to track lot numbers throughout the manufacturing process. This information can be critical for quality control and troubleshooting issues that may arise.
Craftybase is an example of MRP software that features lot tracking functionality while also tracking your inventory levels in real-time. Craftybase lot numbers are automatically assigned to products based on the raw materials used and the production date so that you can see the full traceability of your raw materials through to sale. Sign up for a 14 day free trial today
How does Lot Tracking work in Craftybase?
Using Craftybase, it is possible to track your exact material batch usage from purchase right through to sale.
This is wonderful news for small manufacturing businesses that are required to track manufacture and material provenance information for CPSC and GMP.
Lot numbers can be entered whenever a new batch of materials are purchased. This can be achieved via the Add Expense Item form. In the example below, the Lot Number for this purchase of a single jar of Coconut Oil is 23432DP:
Lot numbers can then be added as part of the manufacture process for each material used. This then provides a direct link between your purchase history and your manufacture history. Continuing the example above, the Coconut Oil material is added to the manufacture for a soap product with the Lot Number of 23432DP to indicate that this particular batch was used in this manufacture:
Finally, order line items can be associated with manufactures, which provides your link between manufactures and orders (see How do I link a manufacture with an order line item? for more details on this process).
The Material Traceability Report can then be used to create a full traceability summary of material usage, displaying all expenses, manufactures and orders that have involved a particular lot of a material.
As you can see from the report, we can identify very quickly that Kyla Olsen has been shipped a product that was manufactured using the 23432DP lot number of Coconut Oil. In the case of a material defect with the oil, this means you can analyse impact and begin recalls immediately, without taking weeks to comb through your records.
The bottom line
Lot tracking is a critical part of traceable record-keeping for any manufacturing business: large or small.
By incorporating lot numbers into your workflow, companies can quickly and easily track items throughout the production process and give you greater visibility of your inventory and stock movements which can be invaluable for quality control and customer service.
Need to get your raw material and product inventory under control?
Try Craftybase - the inventory and manufacturing solution for DTC sellers. Track raw materials and product stock levels (in real time!), lot and batch tracking, COGS, shop floor assignment and much more. It's your small business' production central.