How to Do a Year End Inventory Count as a Small Business
Wondering how to count and value your inventory at end of year? We guide you through the calculations and steps you need to take.
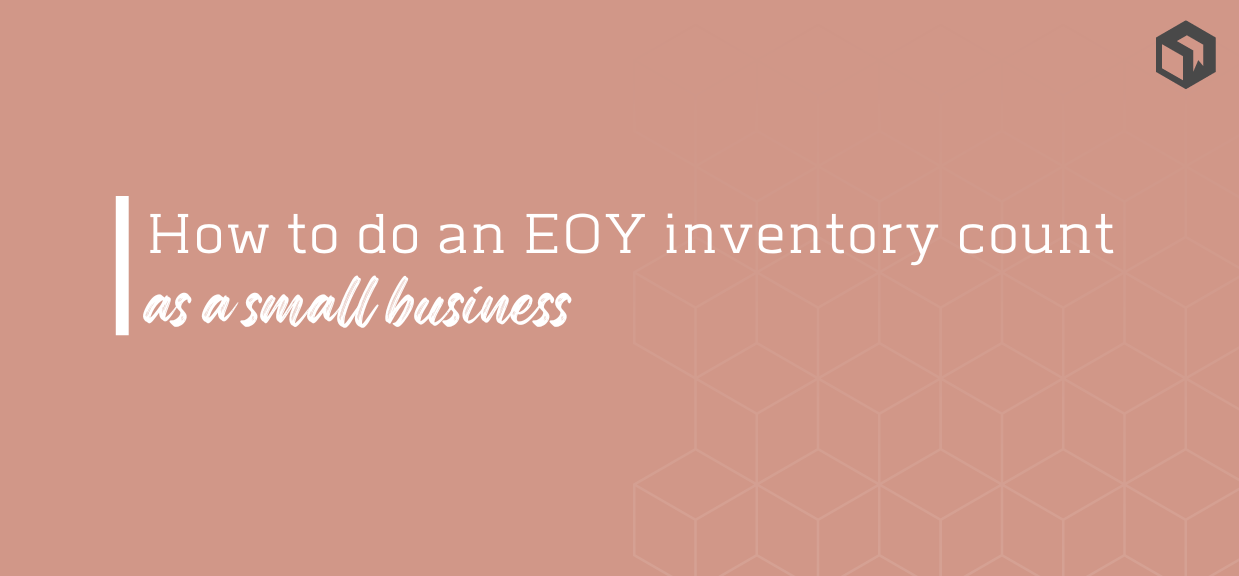
Pat yourself on the back; you’ve just gotten through another silly season of stock flying out the door.
Before you put your feet up, you’ll want to remind yourself that it’s now time to do a year-end physical inventory count. If this takes the spring out of your step and bursts your bubble, you aren’t alone! Year-end stock counts are tedious endeavors and ones that can send your entire business to a complete standstill (that is, if you are doing it wrong 😰).
This guide will explain why end-of-year inventory counts are important, and how you can undertake your stock count (or cycle count). Along the way, we’ll introduce some tools and techniques you can use to make these inventory tasks much faster and less stress-inducing in the future.
Need to get your raw material and product inventory under control?
Try Craftybase - the inventory and manufacturing solution for DTC sellers. Track raw materials and product stock levels (in real time!), COGS, shop floor assignment and much more.
It's your new production central.
What is a year-end inventory count?
Let’s start by defining what we mean by a undertaking an end-of-year inventory count.
At the end of each accounting / financial year, an inventory count is usually taken by a business with inventory to determine three things:
a) how much available, unsold product stock they have on hand;
b) how much raw materials they currently have on hand (if they make products in-house) and;
c) the current value of all stock they have in your possession (aka your inventory valuation).
For resale product businesses, this usually involves counting only products on hand that you haven’t yet sent to your customers.
For in-house manufacturing businesses, an end-of-year count will include both finished products, sub-assemblies, and raw materials yet to be used so can be a much more complex task to undertake.
Depending on how you track your stock, it may be necessary to pause all operations while this end-of-year stocktake is carried out (although, as you will find later in this article, it’s not always the case).
Exactly how you go about each of these tasks depends on how you manage your inventory and calculate unit costs, which we will explain as well along the way.
Why is it important to do an end-of-year inventory count?
Before we delve into the ways you can do your end-of-year count, let’s take a moment to look at the reasons why it is important - particularly for small businesses.
1. To better understand your inventory situation
An end-of-year inventory count is important because it allows you to accurately and definitively measure your stock levels - you don’t need to guestimate your available stock as you have a solid number of working from.
This also means that you can now see if you are under or overstocked and can take the necessary steps to either restock or sell off any excess inventory.
2. To forecast your needs for next year
Understanding your stock situation also allows you to calculate how much stock you have sold throughout the year - this gives you a better understanding of your business’s performance so you can forecast demand for next year.
3. Because…taxes
End-of-year inventory counts, for most, are also performed (often quite reluctantly!) because the tax man requires this information. For sole proprietors in the US, this is reported as Part III of your Schedule C form, whereas for corporations, it’s usually reported on your Form 1125-A: Cost of Goods Sold.
How to perform your stock count
Let’s now take a look at the how of running your end-of-year inventory stock count. There are effectively two methods available to small businesses: the full periodic stock count or the inventory cycle count (or both).
Periodic year-end counting
A year-end periodic inventory count involves a full, comprehensive count of all of the items in your warehouse.
This is usually done once annually and helps to provide an overall snapshot of what products are on hand, how many units there are, and their respective values.
This count is the one you’ll need to stop everything in your business and attend to - it’s important that you have a static number to count: this simply isn’t possible if warehouse staff are running around at the same time picking and packing stock as you go.
Cycle counting
An inventory cycle count on the other hand is a smaller, more frequent form of inventory counting.
It usually involves counting a certain number or type of items on a regular basis (weekly, monthly or quarterly - whatever you decide is a good cadence based on your operations). This allows you to keep track of your stock levels and make sure they are accurate throughout the year.
Cycle counts can theoretically be done manually with inventory systems as simple as paper and pen, however they work best when a company is using an automated system to count inventory, and ideally one that uses perpetual inventory tracking principles.
This is because it’s important to ensure that you are selecting items to count that represent your entire inventory, rather than choosing items randomly.
There are a couple of different ways you can go about choosing your cycle count sample, including standardised random sampling and ABC. Most good perpetual inventory systems will calculate your sample automatically and present this to you on the schedule of your choosing.
Read more: How to do a Cycle Count
What’s the difference between year-end inventory and an inventory cycle count?
To summarise, year-end periodic inventory counts typically provide more detailed information than cycle counts do, as all stock is counted in a single time window.
Cycle counts, as they only require small groups of stock to count, are much easier to factor into small operations as there is no need for a business to shut down completely during a count.
As you can see, how you undertake your end-of-year count is very much dependent on how you wish to track your stock levels and your production team’s capabilities.
How to Calculate your Ending Inventory Value
Just as how you do your actual physical count can differ during the year, so to can the way you calculate your inventory value. This is the figure you will need on your tax return, so it’s wise to make sure you get this right.
Your Ending Inventory Value is the value of your raw materials and the unsold product you have on hand at the end of the year (Dec 31), and is usually calculated using a formula like this:
Ending Inventory = Beginning Inventory + Net Purchases - COGS
Beginning Inventory is essentially your end-of-year figure from last year, and net purchases is the total value of all materials/products you have bought over the financial year.
Your COGS figure can be calculated in a couple of different ways, which we will describe briefly below (for a more in-depth COGS guide, see our article here: How do I calculate COGS?)
FIFO or LIFO
FIFO and LIFO methods have been commonly used as standard ways of valuing inventory; however, as perpetual inventory software systems have gained traction over the years, these valuation methods have waned in popularity. They are still useful for situations where the stock has a short shelf life and different costings - “fast” fashion houses still tend to use LIFO as an example.
LIFO stands for Last In, First Out and calculates your inventory value based on the cost of your older (and often lower) cost remaining stock. It’s, therefore not the most accurate of methods if your stock has increased in cost over time.
FIFO is short for First In, First Out. This inventory valuation method calculates your remaining stock based on a reverse principle to LIFO - your most recent stock purchased is assumed to be the stock in your possession come year-end. This can lead to situations where you overestimate the value of your stock on hand - this becomes particularly clear in recessions where the cost of goods increases sharply.
Average Cost Method
The Average Cost Method is the other way to calculate your EOY inventory value. This method considers all costs associated with purchasing and holding inventory throughout the year, not just for items that have been sold in that time frame. This method is more accurate than the COGS method, but requires more administrative work and can be much more complicated.
Whichever method you choose, both will provide you with an accurate representation of what it cost you to own and maintain your inventory during the fiscal year. With either approach, careful attention should be paid to properly documenting any expenses incurred so that they are accurately accounted for when calculating your tallies.
Read more:
- What is the Average Weighted Cost Method?
- FIFO, LIFO or Average Cost: Which Inventory Valuation Method is Best?
Individual Costed Method
In this method, the cost of each item sold over the fiscal year is calculated independently. This method is typically only used for large ticket items, or for small businesses that make a majority of custom items. It isn’t easy to track and calculate if you have a large product range and/or a large volume of orders.
How inventory management software can make your end-of-year inventory count a snap
Although for small operations it’s completely fine to track your inventory using spreadsheets, for businesses looking to scale perpetual inventory software is the tool that can make your end-of-year count a breeze - it’s basically an automated, and real-time way to track and manage your stock levels and values.
Perpetual inventory software has several advantages over manual inventories:
-
Automatically tracks your inventory as soon as you receive goods into your business, so there’s no need to manually and laboriously update your stock quantities.
-
Allows you to identify which products are selling well and which aren’t so that you can make better-informed buying decisions.
-
You can track your inventory values in real-time so that you have a much better understanding of the value of goods on hand at any given time.
-
Automatically calculates and updates COGS, so you don’t have to waste time manually calculating inventory values.
Using perpetual inventory software can make your end-of-year count a much simpler process. It allows you to easily identify what stock is on hand, what has been sold, and the value of goods remaining at the end of the year. This is invaluable for any business looking to get a clear grasp on their end of year inventory value and stay on top of its finances.
If you’re still counting inventory manually - it’s time to consider investing in perpetual inventory software! The benefits far outweigh the costs, and having accurate and up-to-date data at your fingertips can make a world of difference to your business.
Craftybase is one example of a perpetual inventory system designed for small businesses and can be a vital tool in your belt when it comes to getting your EOY inventory count process done and dusted.
With Craftybase, you can track your stock and materials purchases throughout the year, calculate your COGS accurately and quickly, and keep up-to-date records of all costs associated with maintaining your products.
Using Craftybase’s inventory software, you’ll be able to log your material purchases, manufactures and orders to generate real-time stock levels for both raw and product inventory.
Using the average cost method described above, Craftybase can generate your EOY inventory, including raw materials, sub-assemblies / WIP, and finished products.
All this information is available at just the click of a button come Dec 31st - no more scrambling around trying to figure out what figures you need! Give our free 14-day trial a spin, to see how we can make your December as stress-free as possible.