Best Practices for Managing Your Craft Inventory
Your in-depth guide to successfully managing your craft seller inventory.
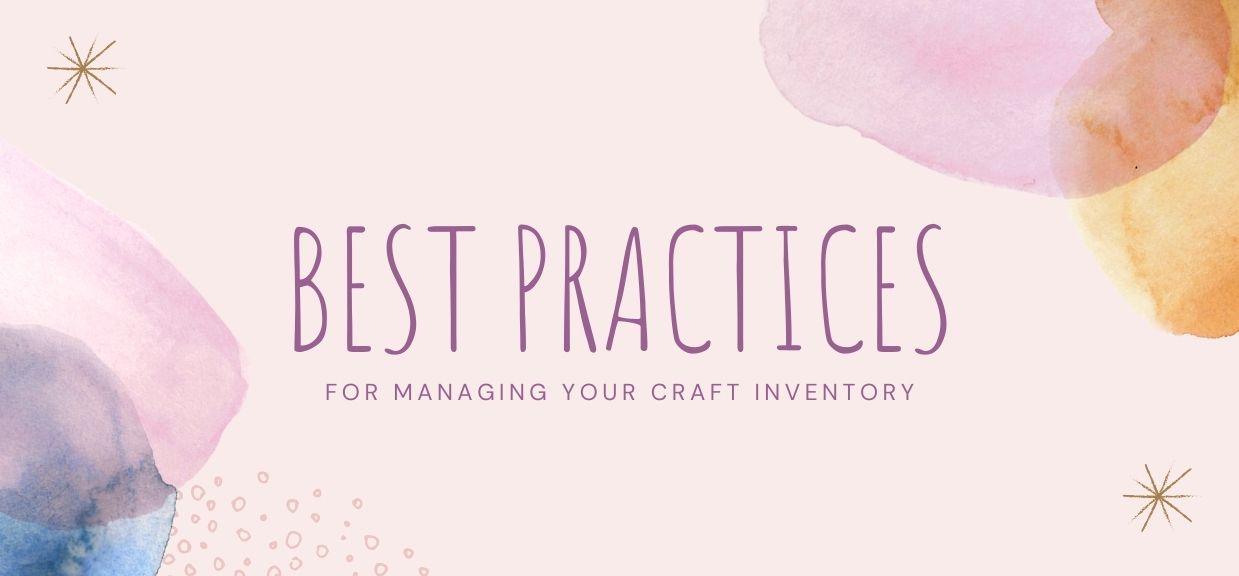
There’s a romanticized view of handmade sellers and artists as being messy, creative whirlwinds. Their clothes and faces are covered in paint, clay or sawdust, with workshops as equally chaotic—materials and half-finished products scattered everywhere.
Because who has time to keep tidy when the muse calls, right?
And while there are makers like that for sure, this isn’t generally a good approach to take: to become a successful seller of your handmade wares, you simply can’t afford to keep a workshop that is disorganized. You can’t lose track of where you keep your materials, supplies, and products. Not when you have a business to run and customers to keep happy.
Ready to take your craft business to the next level?
Try Craftybase: the award winning Etsy inventory software. Track raw materials and product stock, COGS, pricing and much more.
In this post, we explain how to properly manage your inventory and dodge that pesky stereotype so that you can move toward creating a sustainable, well-organized business that will let you make a living from making what you love — while saving you time and effort.
Define your supplies and materials
In a layman’s context, “supplies” and “materials” are sometimes used interchangeably. In a manufacturing context, however, the two are drastically different. Getting them right is important if you want to turn your art into a sustainable business, as it affects your financial projections and tax liability.
Let’s take a look at the difference now:
Materials
Materials are any item or component that is directly used in the production of your handmade craft goods. Some examples to give you an idea are:
- Fabric
- Oil
- Clasps
- Buttons
- Elastic
The rule of thumb is generally: if you use it up when you make something, this is most likely going to be a Material.
Supplies
Supplies, on the other hand, are materials not used directly in the production of goods. These include packaging or shipping-related materials like:
- Envelopes
- Stamps
- Packaging boxes
- Tape
In addition to the above definition, supplies also cover any production materials you use that can’t accurately be measured. Examples include:
- Dye
- Glitter
- Glue
- Thread
See also: What’s the difference between a Supply and a Material? »
Tracking your materials and supplies
Every time you obtain new materials and supplies, you should record it in your inventory management system. This may be a manual process, using paper records or spreadsheets, or an automated one with an entire inventory management platform.
Get a hold of your expenses
As a solo operator, it can be easy to let expenses spiral out of control. You might be too focused on fulfilling orders for customers, or promoting your product. It might be your first time managing a business so you haven’t yet internalized all of the accounting work that has to go on in the background.
Nevertheless, you have to get good at tracking and managing your expenses—fast. And the first step is defining them:
Direct expenses
In manufacturing terms, a direct expense is any cost that is directly associated with producing an item for sale. As a crafting business, direct expenses will represent the majority of your overall expenses.
Direct expenses will generally be included in your COGS (Cost of Goods Sold) calculation.
Indirect expenses
An indirect expense is basically any other business-related expense that is not a direct expense. Electricity, transportation or fuel, website hosting fees, and even depreciation all count as indirect expenses.
On the surface, packaging and shipping might seem to be a direct expense, too, but the reality is that they are not. They’re not used to make the product itself, but they are used to help sell goods and fulfill orders.
Be strategic about your inventory method
There are three primary accounting methods for tracking your inventory, each with their own distinct pros and cons:
FIFO (First In First Out) Method
The FIFO method assumes that the first units of inventory you pick up are also the first ones that are used up or sold. For example, you might create 100 bracelets in January at a cost of $5 each. Then you make another 100 in February for a cost of $6 each.
If you sell 100 bracelets in March, the COGS (cost of goods sold) according to FIFO would be $5 each, because that was the cost of your first batch of 100 bracelets. Only after the first batch is used up would the COGS increase to $6.
FIFO is a more accurate indicator of the value of your ending inventory because the older items are used up first, while your remaining inventory reflects your most recent costs.
LIFO (Last in First Out) Method
The LIFO method is the opposite of FIFO, in that the last units of inventory you make or acquire are the first ones that are used up or sold.
To continue using the bracelets example, when you sell the bracelets in March, your COGS would be $6 each, because those were the latest units created (in February). Your inventory valuation at the end of the period would then be $5 for the remaining bracelets because they were created first (in January).
As you can imagine, this kind of a system isn’t very accurate because given inflation, and the changes that can happen month over month, it’s common to have inventory prices vary, changing the income or profits recorded.
That said, many businesses use LIFO for tax purposes. Purposefully calculating lower profits in this way is a way to take advantage of lower tax brackets without falsifying records.
Rolling Weight Average Method
The rolling weight average method, a.k.a the “moving average” method, recalculates the average value of each inventory item in stock after every purchase. The resulting value tends to fall in between FIFO and LIFO and can be considered fairly conservative.
This method can be very challenging to use with manual accounting methods, so it’s best if you have a suitable accounting or inventory management platform that allows you to easily adjust inventory valuations on a regular basis.
Know when/how to take stock
Knowing what products and materials you have in stock isn’t just crucial for business operations; it’s crucial for financial and tax purposes.
The two main systems for taking stock of inventory are periodic _and _perpetual. Let’s review the differences:
Periodic tracking
Periodic tracking is when you take stock of your inventory levels at least once a year. This is usually done manually (either on paper or using spreadsheet software) by first-time business owners or businesses that don’t have a dedicated inventory management system.
One of the most challenging aspects of this system is associating the final inventory count with price fluctuations of your materials as you bought them throughout the year. The IRS discourages business owners from simply applying a flat value across the entire fiscal period—instead, you have to use a GAAP-approved method such as LIFO, FIFO, or Rolling Average.
Perpetual tracking
Perpetual tracking is essentially calculating inventory levels in real-time. This is only achievable through inventory management software, which automatically logs expenses, orders, and manufactures with every order or transaction.
By updating stock in real-time, you always have a clear picture of your inventory—no more waiting for the end of the year. You’ll have enough info to do profit margin and tax liability analysis (which leads to better business decisions) and you won’t be taken by surprise by low stock. It also saves you the time and effort of having to undergo a huge stocktaking task.
To track your stock levels using a perpetual system almost always requires software. Craftybase is an example of a popular cloud inventory solution designed specifically for small businesses.
Conclusion
We realize that implementing these best practices and changing the way you operate will be difficult—especially if you’ve been running your store for a while now. That change is daunting and may involve a lot of work.
But consider this to be a temporary inconvenience that will save you a lot of headaches later on. With the best practices above, you’ll help your business run smoother, become more predictable, and be more compliant with current tax policies (and therefore less likely to be audited).
Sounds like a good investment to us!