Complete Guide to Raw Material Inventory Management
How to track and manage your raw material inventory to increase profits, become more organized and grow your business.
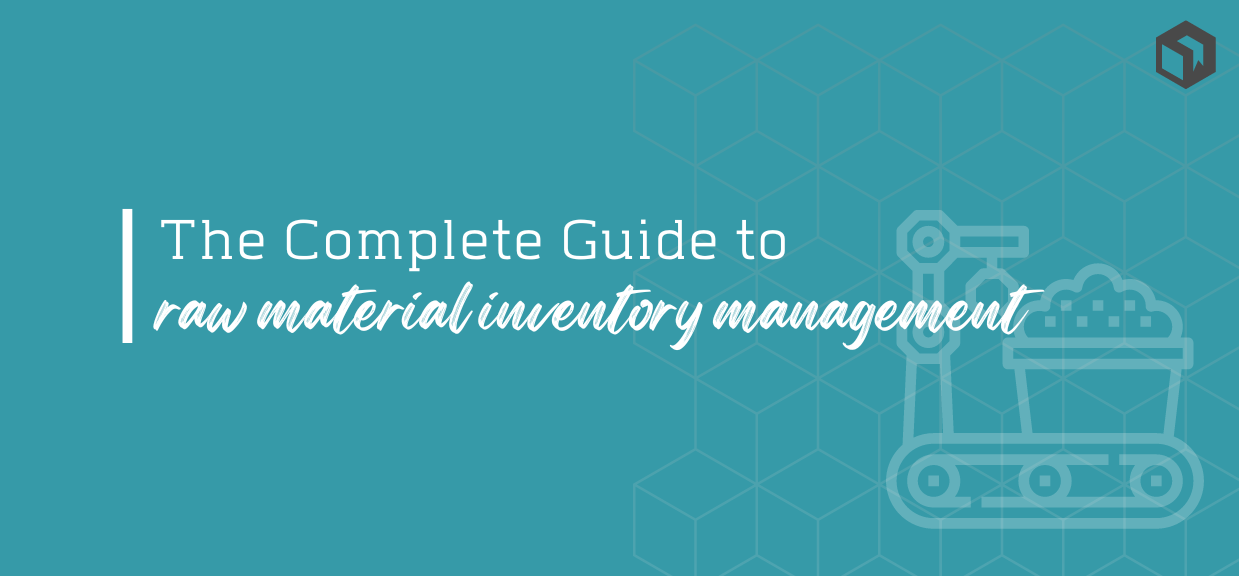
One of the most important aspects of raw materials inventory management is keeping accurate records of your current inventory levels.
This might seem like a no-brainer, but it’s amazing how many businesses don’t keep accurate records of their inventory—or, worse yet, don’t track their inventory levels at all! According to Capgemini, 74% of businesses have experienced a shortage of parts and materials that have at one time impacted on their ability to make and deliver their products, so if you have been in this boat in the past - you are in no way alone.
If you don’t know how much raw materials you have on hand, it’s impossible to effectively manage your inventory. You won’t know when you need to reorder raw materials, and you won’t be able to accurately calculate your raw materials costs.
It can however be an understandably daunting task for small businesses to try and understand what exactly needs to be tracked.
Need to get your raw material and product inventory under control?
Try Craftybase - the inventory and manufacturing solution for DTC sellers. Track raw materials and product stock levels (in real time!), COGS, shop floor assignment and much more.
It's your new production central.
In our ultimate guide to raw material inventory management, we’ll walk you through how to gain control of your raw material processes and show you the methods of calculating your inventory valuations and costings.
We’ll also share some best practices for raw materials inventory management, and explain why it’s so important for small manufacturers.
Let’s get started!
Skip straight to a specific section in our guide:
- What is [raw material](/blog/what-does-raw-materials-mean/) inventory management?
- The importance of tracking your [raw materials](/blog/what-does-raw-materials-mean/)
- Techniques to track your [raw materials](/blog/what-does-raw-materials-mean/)
- [Raw Materials](/blog/what-does-raw-materials-mean/): A Definition
- Perpetual vs Periodic Material Tracking
- Valuation Methods for Inventory
- Inventory Management Terminology you need to know
- Solutions to help you track your [raw materials](/blog/what-does-raw-materials-mean/)
What is Raw Material Inventory Management?
Raw materials are the building blocks that manufacturers use to create their products. If you make soap, for example, your raw materials might include olive oil, coconut oil, lye, and water. If you make furniture, your raw materials might be wood, metal, fabric, and paint.
Tracking your raw materials effectively means keeping accurate records of how much raw material you have on hand at any given time.
This means you need to have a system of monitoring and managing these raw materials throughout your manufacturing process, from the moment they’re ordered to the time they’re used in production (this is referred to as your “supply chain”).
Once you have visibility on your raw material inventory, you can really start to do some “big lever” actions for your business (you know, the ones that REALLY make a difference to your bottom line!). We’re talking things like optimizing your manufacturing processes, fully understanding your costs to manufacture and more.
Why it is important to track your raw materials
Before we get into the nitty gritty of raw materials management, let’s take a quick look at the reasons why you should spend some time creating a proper inventory management strategy for your raw materials.
Keep better track of your outgoings
This one may sound on the surface to be a little obvious, however it’s important to note. Tracking your raw material inventory helps companies keep track of their spending on raw materials. If you don’t know what you have on hand, you simply don’t know what to order. This can lead to ordering stock “just in case” or based on wild estimates: this can really increase your outgoings if you don’t have enough awareness of your processes to guestimate with accuracy.
Avoid stockouts and production delays
If you don’t have enough raw materials on hand, it can lead to production delays while you wait for new materials to arrive. This can be costly in terms of both lost productivity and disappointed customers.
At the worst, you can be left in a situation where you are paying your production team to sit around waiting for your raw material stock to be delivered, while your customer service team is being inundated with impatient and anxious requests for ETAs.
By knowing your raw materials inventory levels, you can avoid these situations by ensuring that you always have enough raw materials on hand to meet your production needs: you’ll be able to place your purchase orders for new materials at the right time to ensure that your production line flows smoothly.
Better manage your cash flow
As a manufacturer, you know that one of your biggest costs is raw materials, so it makes sense to make your cash flow situation for this expense carefully. It’s thus surprising how many companies still rely on guessing their stock levels and thus either stockpiling materials or ordering stock at the last minute.
By tracking your raw materials exact inventory levels (preferably in real-time), you can ensure that your purchase orders are being raised in a predictable and planned fashion.
Identify bottlenecks and inefficiencies in your supply chain
If you’re constantly running out of certain raw materials or find that you have a lot of unused raw materials in your inventory, it could indicate a problem in your supply chain. It’s however almost impossible to figure out where the issue is, if you aren’t creating the right metrics and tracking around your raw materials.
Tracking your raw materials inventory can help you identify these bottlenecks and inefficiencies so that you can take steps to fix them - this leads to improved and streamlined operations that are usually much more cost effective.
Improved decision making
Having accurate and up-to-date information on your raw materials inventory levels can help you make better decisions about a wide range of issues, from pricing to production planning. Instead of relying on “gut feel”, when you start taking control of your raw material inventory situation, you’ll be able to real, substantiated data in order to make decisions that impact on your business.
In a nutshell, tracking your inventory is an absolute no-brainer if you want to create a manufacturing business that grows and makes money.
How do I track my raw materials?
Now that I’ve convinced you on the reasons why you should be tracking your raw materials, the next question is usually - how to do I start getting a decent inventory management strategy in place.
In this section, we’ll briefly touch upon some ways manage your raw material inventory - we’ll be covering these techniques in more detail later in this guide.
Essentially, tracking your raw materials inventory comes down to implementing the following 4 techniques:
- Keeping accurate real-time records of your raw materials inventory levels
- Reviewing and your raw materials inventory regularly (via stocktaking and cycle counting)
- Setting reorder points for all of your raw materials, along with an actionable process when you hit these points
- Analysing and responding to any inventory shrinkage encountered
Let’s now take a deeper dive into some of the terminology you’ll want to be aware of around raw materials inventory management, starting with raw materials.
What is a Raw Material?
As we discussed above, raw materials are the items you use to create your products. These obviously change based on what you make: a watchmaker’s list of raw materials will be very different to a clothing manufacturer.
From an inventory perspective, however, both the watchmaker and the clothing manufacturer will use much the same techniques to track the raw materials in their inventory.
Inventory management is full of terminology, so you’ll encounter several different terms for raw materials depending on the context. Let’s take a look at some of the ways to describe raw materials that you’ll need to be aware of.
Supplies vs Materials
Supplies and Materials are terms are often used interchangeably, but do have specific and different meanings when relating to inventory management.
Supplies are items used in the production process that are not involved to create of the final product. Examples of supplies are items like packaging, shipping containers, and office supplies: they are costs that are important but are completely adjacent to your product making.
Materials, on the other hand, are items that involved directly in creating your final product. Common examples of materials for manufacturing include items like fabric, wood, and metal. The “rule of thumb” here on materials are they tend to be consumable - they are consumed or “used up” either partly or completely when you make a batch of your product.
👉 Want to read more about supplies and materials? Take a look at our detailed explainer here: What’s the difference between supplies and materials?
Direct materials vs Indirect materials
Materials can also be further classified into Direct and Indirect materials.
These terms are often used when discussing the financial aspect of inventory (i.e. as part of your bookkeeping or accounting processes) however are important as they describe the exact role that the item has in your production process.
Direct materials are raw materials directly used to produce your finished goods. This would include things like the fabric in a shirt or the wood used to make a chair.
As described above, they are consumed when manufactured into your product, and your raw material stock levels are decreased each time you produce a new batch. They tend to be relatively easy to quantify (measure) so that you can allocate their usage to each product you make.
Indirect materials, on the other hand, are raw materials involved in the creation of your products that are difficult to fully allocate usage to particular production runs. Indirect materials are usually small, relatively inexpensive and thus difficult to measure and cost.
Examples of indirect materials are things like glue / adhesives, beads or small embellishments, fasteners and disposable tools.
Need to get your raw material and product inventory under control?
Try Craftybase - the inventory and manufacturing solution for DTC sellers. Track raw materials and product stock levels (in real time!), COGS, shop floor assignment and much more.
It's your new production central.
Perpetual vs. Periodic Raw Material Tracking
There are two main ways to track raw materials inventory: perpetual and periodic.
Perpetual tracking is a system where inventory levels are continuously tracked in real-time. This means that you’ll always know exactly how much raw material you have on hand, and you can place orders for more raw materials as soon as your inventory levels start to get low.
The downside of perpetual tracking is that it can be very time-consuming and labor-intensive to track inventory levels in real-time, so it’s not always practical for small businesses. There are however software solutions available that can automate these processes to make them much more streamlined.
Periodic tracking is a system where inventory levels are tracked at set intervals, such as once a week or once a month. The advantage of periodic tracking is that it’s much less time-consuming and labor-intensive than perpetual tracking (other than the constant stocktaking and manual cross checking of stock levels).
The downside of periodic tracking is that you won’t always have an accurate picture of your raw materials inventory levels, which can lead to stock outs or overstocking.
Raw Material Inventory Valuation Methods
There are several different methods for calculating raw materials inventory value: LIFO, FIFO, weighted average costing, and specific identification. It’s important to understand how each inventory valuation method works, so you can confidently choose the right one for your business.
LIFO (Last In, First Out)
LIFO (Last In, First Out) is a raw materials inventory valuation method where the raw materials that were most recently received are assumed to be used first.
This means that the raw materials in your inventory that have been around the longest are assumed to be used last. The advantage of using the LIFO method is that it generally results in a lower raw materials cost of goods sold (COGS) since raw materials costs tend to increase over time.
The downside of LIFO is that it’s not always an accurate representation of reality since raw materials are usually used in the order they’re received (not the other way around).
FIFO (First In, First Out)
FIFO (First In, First Out) is the opposite of LIFO— raw materials are assumed to be used in the order they’re received, with the raw materials that have been in your inventory the longest being used first.
The advantage of FIFO is that it more accurately reflects reality since raw materials are usually used as they’re received. The downside of FIFO is that it generally results in a higher raw materials COGS since raw materials costs tend to increase over time.
Weighted Average Costing
Weighted average costing is a raw materials inventory valuation method where the average cost of all raw materials in your inventory is used to value your remaining raw materials.
The advantage of using weighted average costing is that it provides a more accurate representation of reality since it considers the changing cost of raw materials over time.
The downside of weighted average costing is that it can be more complex to calculate, so you’ll usually need software to handle this task - it is however the technique employed by most manufacturing companies who are looking to scale so it’s worth adopting this method of costing as early as possible.
👉 Read more about inventory valuation methods in our article here: Methods of valuing your inventory
Specific Identification
Specific identification is a raw materials inventory valuation method where each unit of raw material is tracked individually from the time it’s received until the time it’s used in production.
The advantage of using specific identification is that it provides the most accurate representation of reality since you can track each unit of raw material individually.
The downside of specific identification is that it can be very time-consuming and labor-intensive to track each unit of raw material individually, so it tends to not be practical for most businesses, other than exclusively made-to-order operations.
Inventory Management Terminology
Now that we have a good handle on materials and valuation techniques, let’s turn our attention again to raw materials inventory management terminology.
Again, like materials, there is a myriad of terms and techniques you’ll encounter so it’s best to understand as much as you can to make sure you are implementing the best strategy for your manufacturing business. Let’s start with COGS.
COGS (Cost of Goods Sold)
COGS (short for “Cost of Goods Sold”) is a term you’ll often see when discussing inventory and it’s important to understand how it works before we dive into the methods of raw materials costing.
Your COGS is the total cost of all the direct materials (and in some cases, labor) directly used to produce the goods that you sell.
It’s usually calculated as a function of the value of all raw materials in your inventory at the start and end of the year, rather than tallied individually per order or product.
The calculation usually used for COGS is:
COGS = Beginning Inventory + Purchases - Ending Inventory
As two key parts of the COGS formula involve knowing exactly how much raw material stock you had on hand at the beginning and end of your financial period, it’s important that you have an inventory strategy and solution that allows you to calculate these figures with accuracy.
👉 Learn more about how to calculate your Cost of Goods Sold in our primer here: How to calculate your COGS
Reorder Points
A reorder point is the level of raw materials inventory at which you need to place an order for more raw materials. Calculating your reorder points can be tricky, but there are a few factors you’ll need to consider:
-
The lead time for your raw materials: This is the amount of time it will take for your order to arrive after you place it.
-
The safety stock for your raw materials: This is the extra inventory you like to keep on hand in case of unexpected spikes in demand or delays in your supply chain.
-
Your average daily usage of raw materials: This is the average amount of raw materials you use each day in production.
Once you have all of this information, you can calculate your reorder point using the following formula:
Reorder Point = (Lead Time x Average Daily Usage) + Safety Stock
For example, let’s say your raw materials have a lead time of 10 days, you use an average of 200 units per day, and you like to keep a safety stock of 500 units. In this case, your reorder point would be:
Reorder Point = (10 x 200) + 500 = 3,000 units
This means that you should place an order for more raw materials when your inventory levels fall below 3,000 units.
It’s important to note that your reorder point will change over time as your lead time, safety stock, and average daily usage changes. So be sure to recalculate it on a regular basis.
Stocktaking and Cycle Counting your Raw Materials
No matter which inventory valuation method or inventory management process you use, to be successful you’ll need to incorporate a regular habit of combination of regular stocktaking and cycle counts.
Stocktaking is the process of physically counting your inventory to verify that it matches the records you have in your system. This is generally done on a periodic basis, such as once a month or once a quarter.
Cycle counting, on the other hand, is the process of counting a small subset of your inventory items on a regular basis. This allows you to keep a closer eye on your inventory levels and identify any discrepancies sooner.
Both stocktaking and cycle counting are important for ensuring accuracy in your raw materials inventory levels. But cycle counting is generally preferable for smaller businesses since it’s less disruptive and easier to implement.
👉 See how cycle counting can be a game changer for your small manufacturing business: How to Cycle Count your Inventory
Solutions for tracking your raw material inventory
Most manufacturing companies start out tracking their raw materials manually. This usually involves keeping physical inventory records and manually calculating raw materials on hand by either removing stock as it is used from tallies, or stocktaking on a regular basis to determine physical stock on shelf.
If you are looking to scale your small business, tracking things by hand can rapidly become time-consuming and full of errors that are difficult to catch.
Another method commonly used by small manufacturing businesses is to use a spreadsheet. This can be a effective way to track raw materials, as it provides a clear and concise overview of inventory levels. However, it is important to ensure that the spreadsheet is kept up-to-date, as manual updates can lead to errors in your inventory records. It can be difficult to track multiple raw materials in a spreadsheet, and this method is not well-suited for businesses with large or complex inventory needs.
The third option is to use software to track your raw materials inventory. Software solutions for raw materials inventory management typically include features such as:
-
Automatic inventory updates: When you use software to track your raw materials, your inventory levels are automatically updated in real-time whenever a new batch of your products are created. This eliminates the need for manual stocktaking and ensures that your records are always accurate.
-
Cost tracking: Most software solutions will also track the cost of your raw materials, making it easy to see how much you’ve spent on each raw material over time. This can be helpful for budgeting purposes, calculating pricing or negotiating with suppliers.
-
COGS: Some inventory software will also calculate your inventory valuations for your beginning and end of year periods, allowing you to create the numbers you need for your important financial filings.
-
Reporting: Most raw material inventory software solutions also offer reporting features, which can be helpful for tracking your inventory levels over time or identifying trends in your raw materials usage.
By using software to track your raw materials inventory, you can minimize the amount of time and effort required to manage your inventory, while also ensuring that your records are always accurate.
Craftybase is raw materials inventory software designed specifically for small manufacturers that offers all of these features and more. If you’re looking for a comprehensive solution to manage your raw materials inventory, Craftybase can help. Try our 14 day trial today!