What is MRP in Manufacturing and 5 Reasons Why it is Important
This blog post discusses what MRP is in manufacturing and 5 reasons why it is important. MRP stands for materials resource planning and can help businesses keep track of their inventory, production progress, and overall performance. The blog post describes the various benefits of using an MRP system.
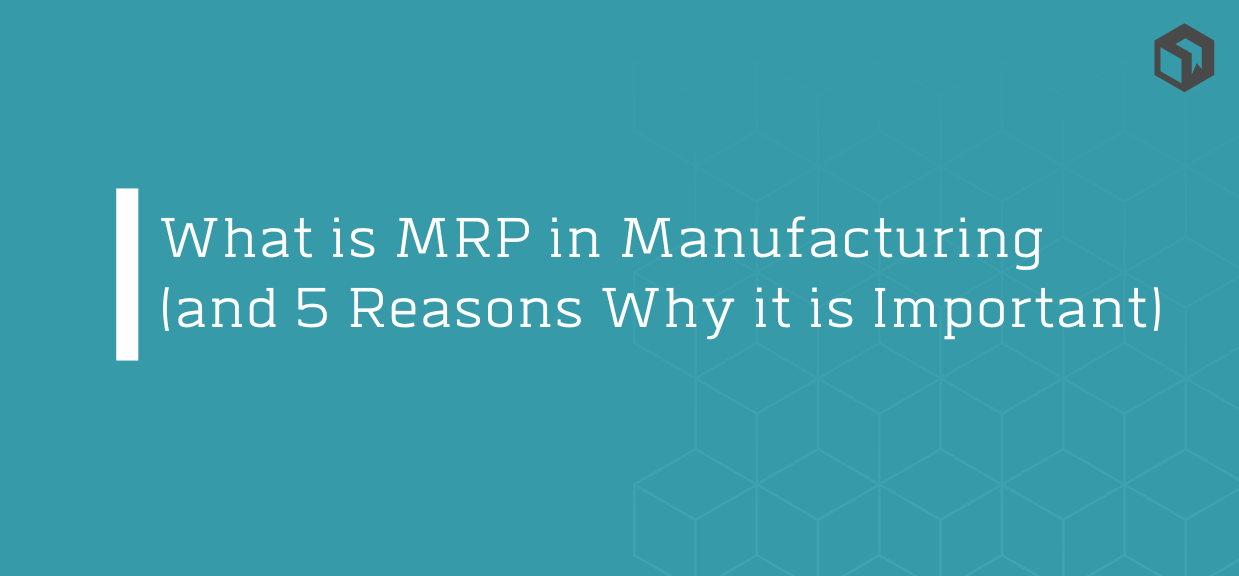
Material resource planning, more commonly known as MRP, is a system used by manufacturers to manage their materials and production effectively.
In this article, we explore the reasons why adopting an MRP system is essential to your small manufacturing business’ success.
Need to get your raw material and product inventory under control?
Try Craftybase - the inventory and manufacturing solution for DTC sellers. Track raw materials and product stock levels (in real time!), COGS, shop floor assignment and much more.
It's your new production central.
What is MRP in manufacturing?
Let’s start with the basics: Material resource planning (sometimes also known as Material requirements planning), or MRP for short, are systems adopted by manufacturers to manage their production effectively.
It’s a multi faceted system that encompasses the following areas of a manufacturing business:
Master Production Schedule: describes when each product should be manufactured
Bill of materials (BOM): a list of the parts required to make each product
Production cycle: details each stage of the production, including exactly when different materials are required
Supplier Lead Times: the estimated time for purchased materials to be delivered from purchase order.
Customer Focus: MRP has a strong customer focus, as everything is measured and optimized to ensure that the customer receives a high quality product within the expected time periods agreed.
Factual Approach: MRP uses metrics and data to guide decision making, and ensures that everyone on the team has access to the same data.
A (short) history of MRP software systems
MRP systems originated in the 1970s as a way to manage inventory and production better. The first generation of MRP systems were manual, paper-based systems that relied on weekly production plans.
With the adoption of computerized systems in the 1980s, this then allowed for real-time updates on stock levels. Nowadays, manufacturers use sophisticated cloud-based MRP solutions to track their inventory and manufacturing activities across countries and devices simultaneously.
There’s often confusion between MRP and ERP systems. Both are software solutions that help manufacturers to manage their business, but they actually serve two different purposes. MRP systems focus on managing the materials and production process, whereas ERP systems encompass a wider range of enterprise resource planning functions such as finance, HR, and customer relationship management.
So, back to MRP systems. The overarching goal of an MRP system is to ensure that the correct materials are available when they are needed in order to avoid production delays.
In order to achieve this goal, MRP systems track three key pieces of information:
-
what materials are required to produce a product
-
when those materials will be needed
-
how much of each material is required
To do this, MRP systems at their core need have solid and robust inventory management capabilities: the ability to track how many raw materials and products you have on hand at any moment in time. They also needs to be able to track the movement of this stock through your entire manufacturing process.
The master production schedule (MPS) is a key component of an production and inventory management system. The MPS details the specific products that need to be produced, as well as when they need to be produced. This information is used to generate what is known as a bill of materials (BOM).
The master production schedule is then used to generate the activities required in order to create the products from raw materials: the purchase orders required for raw materials and components and the manufacturing orders (MO) for the shop floor production team.
Why should small manufacturers use an MRP system?
Although it may seem like it’s a good idea to start with a spreadsheet to track your inventory and manufacturing activity, if you have any aims to scale your manufacturing business you’ll quickly find you outgrow this solution.
It’s therefore important to choose an MRP system that allows you to grow your manufacturing operations in a way that ensures that you and your staff always have a clear picture of your stock levels and what is required in order to get those products out the door.
Let’s go through five big reasons why your small manufacturing business needs to start using an MRP system:
1. MRP systems help small manufacturers save time and money by reducing the need for surplus inventory.
By knowing what raw materials and components are needed to produce a product, as well as exactly when they will be needed, manufacturers can ensure that they are ordering only the necessary amount of each material.
This has obvious advantages to your business cashflow - by ensuring that you only buy what you need you’ll be able to direct your cash reserves to grow your business in other directions.
This also reduces the amount of inventory that needs to be stored. If you are paying for your warehouse space by the square foot, minimizing the amount of space you are taking up with raw materials that you may or may not use in the future should be a no-brainer.
2. MRP systems help manufacturers avoid production delays.
By ensuring that the correct materials are available when they are needed, manufacturing resource planning systems help avoid production delays caused by waiting for materials to arrive.
Having a predictable and reliable master production schedule means that your team can plan their time. As a small business owner, this has obvious cost savings for labor and can ensure that your team is working effectively.
If you sell DTC, avoidable production delays can also be the source of customer frustration. Ensuring you are managing your master production schedule and ensuring orders get out in time is essential in a time where reviews can make or break a small business.
3. MRP systems help businesses keep track of production progress.
By tracking what materials are needed and when they are needed, MRP systems provide everyone in the team with a clear picture of where all orders are at: from purchases of raw materials to completed finished products about to go out the warehouse door.
Having full visibility of your inventory management situation means you can identify and address manufacturing issues quickly, and improve your delivery times.
You can also use an MRP system to identify direct cost savings. From which vendor has the lowest cost materials, and how to make your product faster without sacrificing quality, these insights can all be generated from your MRP system.
4. MRP systems improve communication between your team
Because MRP systems track information about what materials are required and when they will be needed, they can help different teams within a DTC manufacturing company communicate more effectively.
For example, if the support team knows that a customer has placed an order for a product that is not currently in stock, by checking the MRP they can communicate estimated lead times to the customer and manage expectations.
5. MRP systems can help businesses better manage their supply chain and ensure that materials are being delivered on time.
By tracking what materials are needed for current production and when the materials will be needed, businesses can use MRP software to optimize their supply chain and ensure that the materials are being delivered in a timely manner.
This is especially important for businesses that operate on Just-In-Time (JIT) inventory systems, where inventory is typically only ordered and received as it is needed for production.
By managing their supply chain effectively, businesses can avoid production disruptions and ensure that their customers are receiving the products they need when they need them.
If you have ambitions to grow your manufacturing company, choosing an MRP system that can accommodate growth is essential.
The last thing you want is to have to change your entire manufacturing process and invest in a new MRP system because the one you are using can no longer cope with increased demand.
An MRP system that can be easily scaled will save you time and money in the long run, and allow you to focus on what’s important - growing your business.
Overall, MRP is a powerful tool that can help small manufacturing businesses improve their production efficiency and reduce their costs. When used properly, MRP can help businesses keep track of their inventory, production progress, and overall performance.