What does a Subassembly Mean on a Bill of Materials? Definitions and Explanations
We cover what a subassembly is and how it can be used to improve your manufacturing process. We also discuss how you can use multi-level bill of materials to track subassemblies.
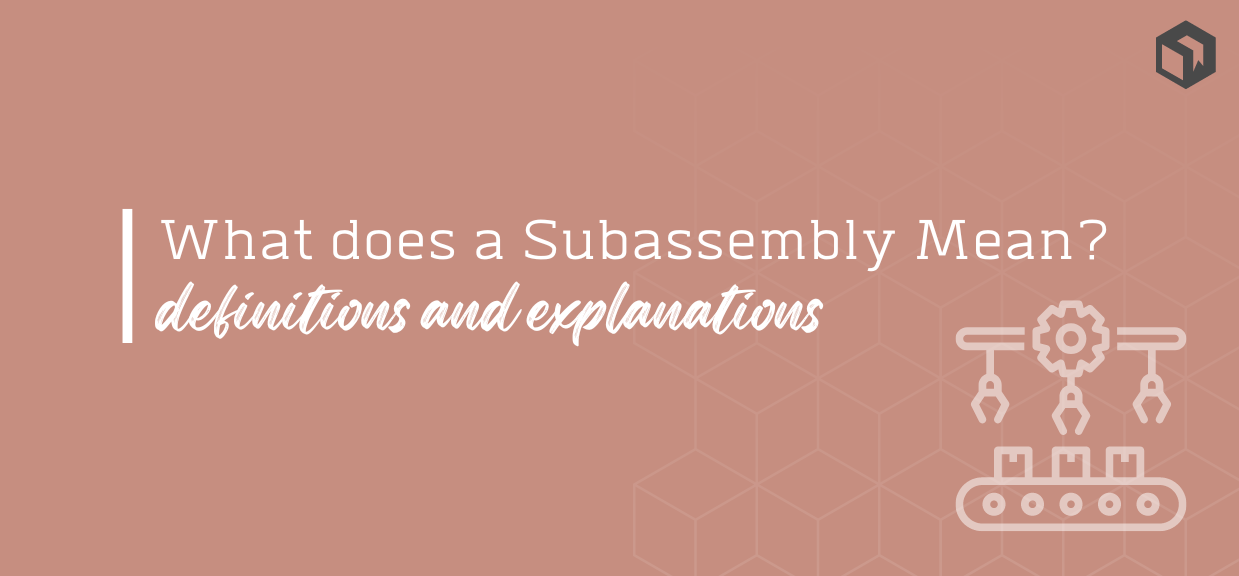
When you are putting together a bill of materials for your product, it is important to understand what all of the terms mean. One term that you may come across is “subassembly.”
This can be confusing if you don’t know what it means. In this blog post, we will define what a subassembly is and how you can structure your bill of materials to better track the steps in your production process.
Need to get your raw material and product inventory under control?
Try Craftybase - the inventory and manufacturing solution for DTC sellers. Track raw materials and product stock levels (in real time!), COGS, shop floor assignment and much more.
It's your new production central.
What is a subassembly?
An assembly is a group of parts that are put together to form a complete unit.
A subassembly is thus a part of an assembly - it is a group of parts that are put together to form a smaller unit within the larger assembly.
Sub assemblies are important because they allow manufacturers to break down the production process into smaller, more manageable steps. This can have a number of benefits to your manufacturing process, which we will explain in detail below.
Creating a bill of materials with sub-assemblies
When you are creating a bill of materials for your final product, it is important to understand what subassemblies are and how they fit into the overall production process.
What is a Bill of Materials? Examples for small manufacturers →
As we have mentioned, subassemblies are important because they allow manufacturers to break down the production process into smaller, more manageable steps. This can make the manufacturing process easier to track, to plan production and staffing for, and also to analyze to find ways of optimizing and improving your supply chain.
Let’s say that you are a bicycle manufacturer. To create a bicycle, you might have a list of materials that looks something like this:
- Frame
- Wheels
- Tires
- Brakes
- Seat
- Handlebars
Let’s say for the wheels that you also make these in-house, however, all other materials are purchased from supplies. This means you’ll want to create two bill of materials: one for the wheel subassembly and another for the parent bicycle finished product.
The wheel subassembly can now be produced at any time as it has its own raw material list and labor estimates - it can stand alone as manufacturing step in its own right.
The bicycle bill of materials now only needs to list the “wheel” as a material (or component) and does not need to list all raw materials for this subassembly.
Creating bill of materials with sub-assemblies is also useful as it allows you to track labor costs through the whole production process. This information is important to better understand your profit margins and make better pricing decisions.
Check out our free BOM template for Excel and Numbers here →
How multi level Boms help track sub-assemblies
A multi level bill of materials handles both parent finished products and their sub-assemblies. You can theoretically create many stepped levels of subassembly BoMs within a multi level BoM, each representing a key independent part of the production process.
If you just had a single level bill of materials, it would be difficult to track which parts went into each subassembly as all materials would appear in the list. However, if you structure your products to have a multi level bill of materials, it’s much easier to see the steps of your process and the raw materials required for each.
This can be helpful if you need to troubleshoot a particular subassembly. For example, let’s say that you have a problem with subassembly C. If you have created a multi level bill of materials, you can easily see which parts are in subassembly C. This can help you narrow down the problem and find a solution more quickly.
Using software to track and create multi level boms for your assemblies
While you can technically use a spreadsheet to create and track multi level bill of materials, this can quickly become complicated and difficult to manage as you add more production steps.
Instead, we recommend using specialized software designed for managing assemblies and bills of materials - this is usually a feature-set found in ERP or MRP systems. This type of software will make it much easier to create, track, and optimize your production process.
One example of this type of software is Craftybase MRP. With Craftybase, you can easily create multi level bills of materials for your product assemblies.
You can also use Craftybase to track production progress and manage your raw inventory and finished product stock. Try for free today.